About Aluminum Casting Fundamentals: Whatever You Required to Know
About Aluminum Casting Fundamentals: Whatever You Required to Know
Blog Article
From Design to Finish: The Full Aluminum Casting Process Demystified
In the realm of production, the process of aluminum spreading stands as an essential approach that has fueled sectors for years. Each action in this intricate process, from the first design stage to the last finishing touches, plays an essential function in forming the end result of the item. What absolutely exists below the surface of this procedure stays an enigma to several. By deciphering the complexities and clarifying the nuances associated with each stage, a much deeper understanding of the art and scientific research behind light weight aluminum spreading emerges. about aluminum casting. Remain tuned as we explore the complete light weight aluminum spreading procedure, revealing the details that transform basic materials right into polished products.
Designing the Casting Mold And Mildew
When initiating the aluminum casting process, thorough attention to creating the casting mold is paramount for ensuring the final product's honesty and top quality. The casting mold and mildew acts as the foundation for the whole spreading process, dictating the shape, measurements, and surface area coating of the ultimate aluminum part.
To make an efficient spreading mold, engineers must think about different elements such as the complexity of the part, the kind of light weight aluminum alloy being utilized, and the desired properties of the last item. about aluminum casting. Computer-aided design (CAD) software is typically employed to create thorough schematics of the mold, enabling specific personalization and optimization
Moreover, the layout of the spreading mold directly impacts the performance and cost-effectiveness of the casting process. A properly designed mold and mildew decreases product waste, reduces the demand for comprehensive post-casting machining, and improves total manufacturing rate.
Melting and Pouring Light Weight Aluminum
With the style of the casting mold and mildew settled, the following essential action in the light weight aluminum casting procedure is the melting and pouring of the aluminum alloy. The process starts with packing the aluminum alloy right into a furnace where it is heated up to its melting point, typically around 660 ° C(1220 ° F) for aluminum. Crucible heating systems, induction heating systems, or gas-fired reverberatory heaters are generally utilized for melting light weight aluminum. Once the light weight aluminum is liquified, it is critical to preserve the temperature within a particular array to ensure the quality of the castings.
After the light weight aluminum reaches the wanted uniformity, it is time for putting. The liquified aluminum is very carefully transferred from the heater to the casting mold. This step requires accuracy and control to prevent flaws in the last item. The putting process should be executed quickly to stop early solidification and ensure the light weight aluminum loads the mold and mildew completely. Proper pouring methods contribute considerably to the total quality of the last aluminum casting.
Strengthening and Cooling Refine
Upon completion of the putting process, the molten light weight aluminum transitions into the cooling and strengthening phase, a vital phase in the light weight aluminum spreading procedure that directly impacts the end product's stability and qualities. As the aluminum begins to cool down, its molecules prepare themselves into a solid form, progressively taking on the form of the mold and mildew. The price at which the light weight aluminum cools is essential, as it affects the material's microstructure and mechanical homes. Quick cooling can lead to a finer grain framework, enhancing the material's toughness, while slower air conditioning might cause bigger grain sizes, influencing the end product's ductility.
During this stage, it is crucial to manage the cooling procedure carefully to stay clear of defects such as porosity, shrinkage, or interior anxieties. Numerous cooling approaches, such as air cooling, water quenching, or controlled air conditioning chambers, can be used based on the details requirements of the casting (about aluminum casting). By monitoring and regulating the solidification and cooling down process, makers can guarantee the manufacturing of high-grade light weight aluminum spreadings with the desired mechanical and metallurgical residential or commercial properties

Eliminating the Final Casting
Once the aluminum spreading has actually completely solidified and cooled down in the mold, the next action in the process entails meticulously getting rid of the last casting. This step is critical to make sure that the aluminum part is effectively removed with no damages or defects.
To get rid of the casting, the mold and mildew is opened, and the casting is removed utilizing numerous techniques depending on the intricacy of the part and the mold layout. For simpler shapes, the spreading can frequently be conveniently removed by hand or with easy devices. However, for even more elaborate designs, added devices such as ejector pins, air blasts, or hydraulic systems may be called for to assist in the removal procedure without triggering any type of injury to the spreading.
After the spreading is successfully eliminated from the mold and mildew, any kind of excess product such as gateways, joggers, or risers that were made use of during the spreading process are trimmed off. This step helps in accomplishing the final preferred shape of the aluminum part prior to it undergoes any kind of extra completing processes.
Finishing and Quality Evaluation
The last in the aluminum spreading procedure includes careful completing techniques and extensive top quality inspection procedures to guarantee the integrity and precision of the actors aluminum components. Finishing techniques such as grinding, fining sand, and shot blasting are utilized to remove any kind of excess product, smooth harsh surface areas, and boost the visual appeal of the end product. blog here These processes not only boost the look yet likewise make certain that the components satisfy the company website defined dimensional tolerances and surface area finish requirements.
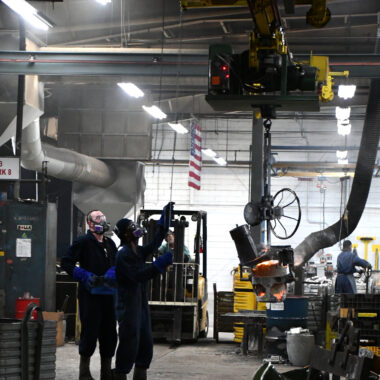
Final Thought
To conclude, the aluminum spreading process involves making the mold and mildew, melting and putting light weight aluminum, solidifying and cooling the spreading, eliminating the end product, and finishing with a top quality evaluation. Each step is essential in guaranteeing the last product fulfills the desired specifications. By recognizing the entire procedure, producers can create high-grade light weight aluminum spreadings successfully and properly.
Stay tuned as we study the full light weight aluminum casting procedure, revealing the intricacies that transform raw materials into polished products.
With the design of the casting mold and mildew settled, the following important action in the aluminum casting procedure is the melting and pouring of the light weight aluminum alloy.Upon conclusion of the pouring procedure, the molten light weight aluminum transitions into the solidifying and cooling phase, a vital stage in the light weight aluminum spreading procedure that straight impacts the final product's stability and attributes.The final stage in the aluminum spreading process includes thorough finishing strategies her latest blog and strenuous top quality evaluation procedures to make sure the honesty and precision of the actors aluminum components.In final thought, the light weight aluminum casting procedure entails developing the mold, melting and pouring light weight aluminum, strengthening and cooling the spreading, eliminating the final product, and finishing with a high quality assessment.
Report this page